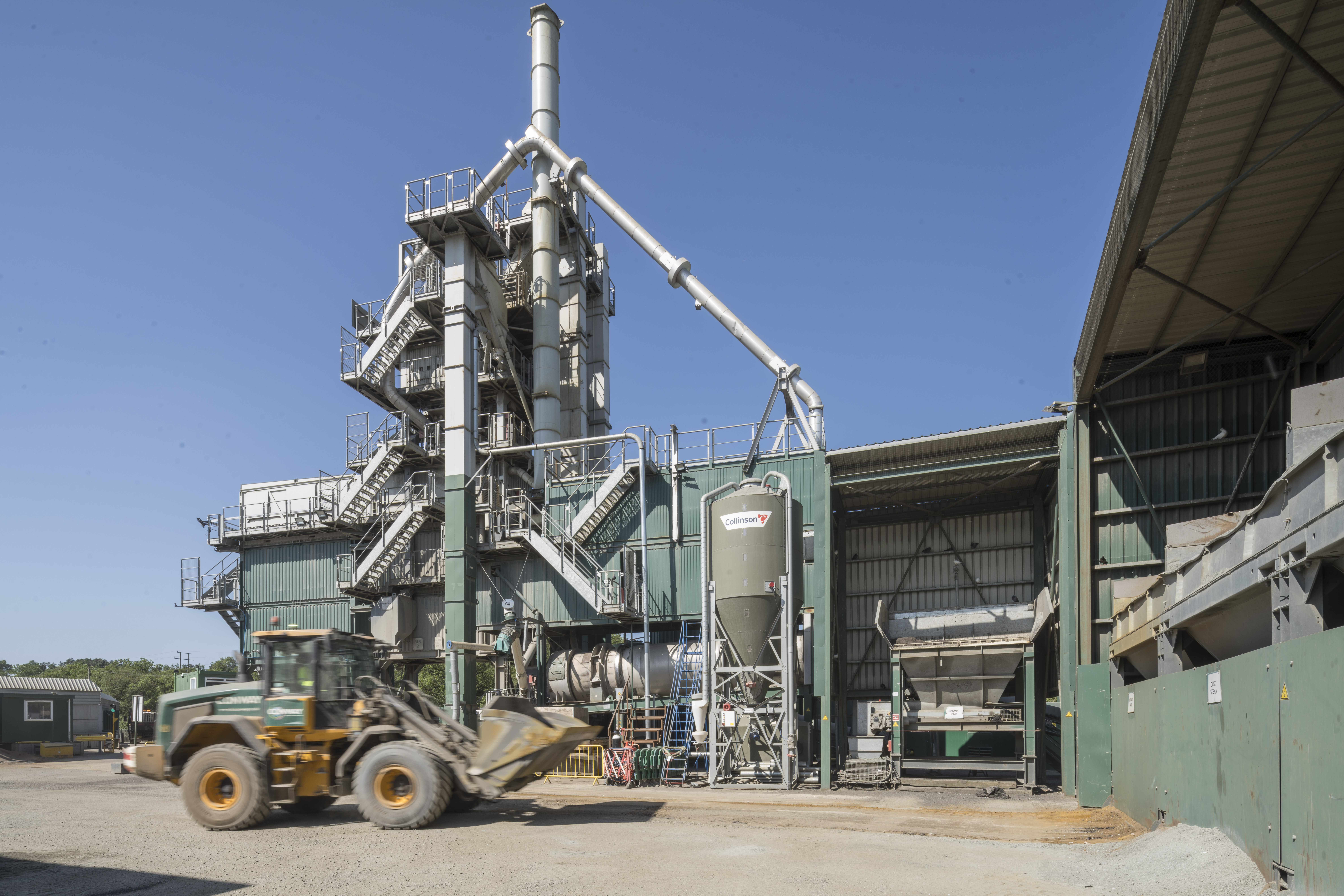
The Marketing team is back with another blog, this time paying a visit to our Aldershot asphalt plant for an exclusive behind-the-scenes look.
Proactive Maintenance, Plant Improvements, and Staff Development Drive Long-Term Gains
Overview: Following a three-week maintenance shutdown in January, the Heathrow Asphalt Plant team has diligently completed critical upgrades and invested in training to enhance operational efficiency.
This case study highlights the major achievements during this downtime and the impressive improvements made to plant operations by our great people, leading to a significant increase in production capabilities, particularly regarding Recycled Asphalt Product (RAP).
Key Achievements During Shutdown:
Plant Upgrades and Maintenance: During the maintenance period, several critical upgrades and improvements were made, significantly enhancing the plant’s operational capabilities.
Key work completed included:
These upgrades, particularly to the baghouse, mixer box, and RAP screw system, had an immediate and profound impact on production, notably during Hot RAP runs.
The implementation of the mixer box exemplifies FM Conway’s long-standing commitment to plant improvement and health and safety risk reduction, particularly addressing Confined Space, one of our Big 10 Risks.
Staff Training and Development: During the three-week closure, 95% of staff completed mandatory training, including First-Aid Training, Health and Safety courses, and Machine Operational courses.
In addition, two full-time Weighbridge Clerks were sent to our Sevenoaks head office to gain exposure to order processing within the Customer Service team. Other staff members spent time with internal Drivers to understand the logistics behind the dispatch and laying of asphalt.
The team also assisted sister plants with additional work that had accrued due to the closure.
This included:
Results:
The infrastructure improvements led to a significant increase in production efficiency. Notably, the new RAP screw system and improved mixer box led to a 30-50% increase in production during Hot RAP runs. The plant was able to achieve 300 tonnes per hour during a Hot RAP run with 70% recycled materials, a feat that would not have been possible with the previous system.
The ability to quickly manage the weigh hopper doors after just four to five batches and push the system harder during RAP runs has unlocked new potential. Future plans involve testing minor tweaks to various areas of the plant, including:
These enhancements are expected to further improve production rates and efficiency.
Infrastructure Improvement:
Additionally, a new drainage system was installed in the aggregate bays area, which had been prone to flooding during heavy rainfall. The area was resurfaced, and the new drainage system has successfully redirected water away from previously affected areas, providing a safer environment for vehicle tipping.
Conclusion:
The combination of staff development, cross-training, and extensive plant upgrades during the maintenance period has resulted in improved plant performance and an upskilled workforce.
The plant's ability to achieve more efficient production rates, particularly during Hot RAP runs, has positioned it for continued success in a competitive market. The ongoing adjustments and minor tweaks expected in the coming weeks will likely further elevate the plant’s operational capabilities, ensuring it remains a high-performance facility for years to come.
Thank You to Our Great People:
Thank you to the Engineering and Operations teams, as well as everyone involved, for your hard work and dedication. Your efforts have truly made a difference!